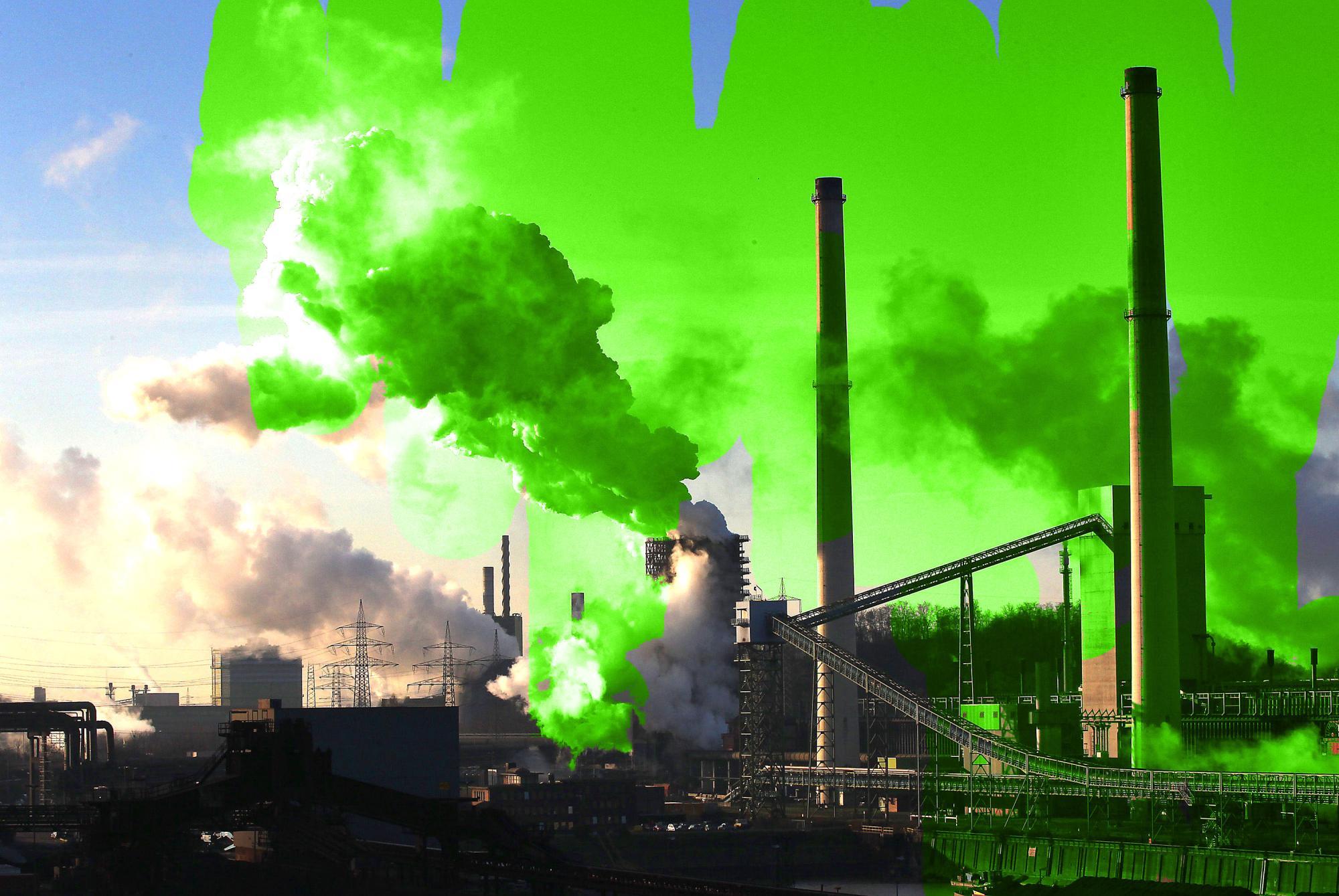
Die Transformer: Wie sich Unternehmen neu erfinden
28 Millionen Tonnen – so viel stieß die heimische Industrie im Jahr 2021 aus. Bis 2040 soll dieser Wert auf null gebracht werden. Denn ab dann soll Österreich, so steht es im Regierungsübereinkommen der türkis-grünen Koalition, klimaneutral sein.
Ein ambitioniertes Ziel. Höchste Zeit also, dass sich die Unternehmen überlegen, wie das gehen soll. Denn so utopisch, wie manch einer vielleicht glauben mag, ist das Vorhaben nicht. Ein Konsortium namens NEFI (New Energy for Industry) – dem zahlreiche Forschungsinstitute und Unternehmen angehören – veröffentlichte kürzlich eine Studie, der zufolge der Umstieg zwar einige Kraftanstrengung braucht, aber tatsächlich möglich ist. Und zwar mit bekannten und bereits vorhandenen Technologien. Hürden orten die Studienautoren in den rechtlichen und politischen Rahmenbedingungen.
Was auffällt: In vielen Fällen sind die produzierenden Unternehmen in ihren Bemühungen in Sachen Klimaschutz oft deutlich fortschrittlicher als die Politik. Vier Beispiele.
Neu gebrannt: WIENERBERGER
Der Ziegelhersteller war früh dran: Er verordnete sich bereits vor 15 Jahren eine Nachhaltigkeitsstrategie, also Ende der 2000er-Jahre, als nur wenige überhaupt etwas mit dem Begriff anzufangen wussten. Wienerberger begann damals, die Ziegel so zu designen, dass sie möglichst wenig Material verbrauchten, und den Gasverbrauch beim Brennen möglichst weit herunterzuschrauben. Jetzt stößt das Unternehmen in eine neue Dimension vor: Im oberösterreichischen Uttendorf wird demnächst der weltweit größte industrielle Elektroofen zur Ziegelproduktion gebaut. Der alte Gasofen wird gerade abgerissen. „Wir haben den letzten Ziegel, der im Juli in Uttendorf klassisch gebrannt wurde, aufgehoben und werden ihn in eine Vitrine stellen“, sagt Johann Marchner, Chef von Wienerberger Österreich, in der aktuellen Folge des Tauwetter-Podcasts. Ende 2024 wird das Gerät in den Testbetrieb gehen, ab 2025 soll es regulär laufen. „Wir haben nicht einfach den alten Ofen genommen und die Gasbrenner ausgetauscht, sondern gemeinsam mit dem Austrian Institute of Technology eine neue Technologie entwickelt“, sagt Marchner. Deshalb benötigt der Elektroofen 30 Prozent weniger Energie als sein Vorgänger, betrieben wird er mit Ökostrom. Insgesamt will Wienerberger in dem Werk 90 Prozent der bisher verursachten CO2-Emissionen einsparen.
30 Millionen Euro kostet die Umstellung der Produktion, finanziert hat das hauptsächlich Wienerberger selbst. Um weitere Standorte in Österreich umzurüsten und den -Ausstoß bis 2030 insgesamt um 50 Prozent zu senken, muss Wienerberger noch einmal mehr als 200 Millionen Euro in die Hand nehmen. „Wir werden diesen Weg gehen. Die Dekarbonisierung ist alternativlos“, sagt Geschäftsführer Marchner. Aber die Ziegel werden dadurch teurer werden. Um trotzdem konkurrenzfähig zu bleiben, wünscht er sich von der Politik endlich brauchbare Rahmenbedingungen, etwa bei den Gebäuderichtlinien. „Wir müssen verhindern, dass Baustoffe mit großem -Fußabdruck einen kaufmännischen Vorteil haben.“
Generell macht dem Wienerberger-Chef das Stromleitungsnetz in Österreich Sorge, das für die Transformation der Industrie in Richtung Erneuerbarer viel zu schwach ausgebaut ist. „Ich verstehe nicht, warum die Politik hier nicht einfach einen Masterplan macht. Sie braucht nur alle Beteiligten an einen Tisch bringen und die Großindustrie fragen, was diese benötigt“, sagt Marchner. Danach könne man die Infrastruktur zügig ausbauen – unabhängig von Parteien und Bundesländern. „Ich verstehe nicht, warum nichts weitergeht. Es geht hier nicht um Einzelinteressen, sondern um den Aufbau einer nachhaltigen Industrie in ganz Österreich.“
PET und Pfand: VÖSLAUER
Wenn in Österreich Preise für Nachhaltigkeit zu vergeben sind, steht der Mineralwasserabfüller Vöslauer meist in der ersten Reihe: Für seinen Nachhaltigkeitsbericht wurde er mit dem Austrian Sustainability Reporting Award prämiert, für seine 0,5-Liter-Glasflasche erhielt er den Staatspreis Smart Packaging, und 2021 wurde er als „Nachhaltige Gestalter*in“ ausgezeichnet. Das kommt nicht von ungefähr: Nachhaltigkeit und Klimaschutz gehören seit mehr als 15 Jahren zur Firmenphilosophie. Geschäftsführerin Birgit Aichinger formuliert das so: „Als Unternehmen müssen wir Teil der Lösung sein. Unser Anspruch ist, jedes Produkt nachhaltiger als seinen Vorgänger zu gestalten.“
Das 1936 gegründete Unternehmen mit Sitz im namensgebenden Bad Vöslau dominiert den heimischen Markt: 300 Millionen Liter Quellwasser und Erfrischungsgetränke werden pro Jahr abgefüllt – damit hält man 40 Prozent Marktanteil. Vöslauer war oft Vorreiter: 2014 führte man als erster Hersteller die Ein-Liter-Glas-Mehrweg-Flasche wieder ein. 2018 brachte man die erste Flasche aus 100Prozent recyceltem PET (rePET) auf den Markt. 2020 wurde das gesamte Einweg-PET-Sortiment auf rePET umgestellt – fünf Jahre früher als ursprünglich geplant. „Wir waren 19 Jahre lang die einzigen Anbieter in Österreich mit einem PET-Pfandsystem. Im vergangenen Frühjahr haben wir es durch eine moderne Version der PET-Mehrwegflasche ersetzt“, erzählt Aichinger. Diese könne etwa zwölf Mal wiederbefüllt werden und drei bis vier Jahre in Verwendung bleiben. Damit werden rund 80 Prozent Material und 420 Tonnen pro Jahr eingespart.
Insgesamt hat Vöslauer seit 2005 50 Prozent seiner -Emissionen aus eigener Kraft reduziert. Dazu beigetragen haben auch eine Photovoltaik-Anlage mit mehr als 8000 Quadratmetern, die ein Fünftel des Strombedarfs deckt, sowie der Bezug von Ökostrom. Die verbliebenen 50 Prozent wurden durch Klimaschutzprojekte kompensiert. „Seit 2020 sind wir als Unternehmen und mit unseren Produkten -neutral“, sagt Aichinger. Doch das Unternehmen will noch mehr: Bis 2030 sollen die Treibhausgas-Emissionen im Vergleich zu 2019 um 28 Prozent reduziert werden, der Anteil an Mehrweggebinden soll auf rund 40 Prozent verdoppelt werden.
Jute statt Plastik: INFINEON
Es macht ein bisschen den Eindruck, als hätte jemand die Überreste von Jutesackerln einer neuen Verwendung zugeführt. Und ganz so falsch dürfte die Assoziation nicht sein. Der deutsche Chiphersteller Infineon stellte kürzlich ein neues Produkt vor: recycelbare Leiterplatten, deren Trägermaterial auf Naturfasern basiert. Dieses sogenannte Leiterplattensubs-trat wurde von einem britischen Start-up entwickelt und ist biologisch abbaubar. Taucht man es in heißes Wasser, löst es sich auf und lässt nur kompostierbares Material zurück. Damit soll ein Beitrag zur Reduktion von Elektroschrott (von dem jährlich weltweit rund 50 Millionen Tonnen produziert werden) und -Emissionen geleistet werden. Laut Herstellerangaben können damit bei Leiterplatten bis zu 60 Prozent des Treibhausgas-Ausstoßes vermieden werden. „Derzeit setzen wir das neue Material für erste Demo- und Evaluierungsboards ein“, erzählt Andreas Kopp, Leiter des Infineon-Produktmanagements am Standort Villach.
Elektroschrott-Reduktion
In den Infineon-Prüflabors in Villach werden die recycelbaren Leiterplatten untersucht.
In den dortigen Prüflaboren wird nun untersucht, wie und wo das Material verwendet werden kann beziehungsweise wo seine Grenzen sind. Etwa wie sich hohe Temperatur und hohe Luftfeuchtigkeit in Kombination auf die recycelbaren Leiterplatten auswirken. Denn, so Kopp, die elektrischen und thermischen Eigenschaften dürften nicht beeinträchtigt werden. Infineon hat drei verschiedene Modelle für unterschiedliche Anwendungen hergestellt, die bereits in mehr als 500 Einheiten im Einsatz sind. Darunter etwa auch ein Board mit Komponenten speziell für Kühlschrankanwendungen. „Mit den gewonnenen Erkenntnissen können wir dann unsere Kunden bei einem Umstieg auf dieses Material unterstützen“, sagt Kopp. Außerdem werde erforscht, ob auch die Wiederverwendung einzelner Komponenten der elektronischen Bauteile möglich ist: „Das wäre ein weiterer Schritt auf dem Weg zur Förderung einer Kreislaufwirtschaft in der Elektronikindustrie.“
Heavy Metal: VOESTALPINE
Die Stahlindustrie bläst Unmengen von in die Luft. Mit 9,4 Millionen Tonnen stieß die voestalpine allein in ihrem Hauptwerk in Linz 2021 mehr Treibhausgase aus als 900.000 Österreicherinnen und Österreicher zusammen. Das soll sich nun ändern: Nächstes Jahr beginnt der Bau zweier Elektrolichtbogenöfen in Linz und Donawitz, die 2027 in Betrieb gehen sollen. Die Emissionen der voestalpine werden damit um 30 Prozent sinken – das wären immerhin fast fünf Prozent des gesamten -Ausstoßes Österreichs.
Der Stahl soll ergrünen
1,5 Milliarden Euro werden in Elektroöfen investiert. PV- Anlagen liefern Strom.
Ab 2030 ist die Ablöse von zwei weiteren Hochöfen in Linz und Donawitz sowie die Investition in einen weiteren Elektrolichtbogenofen in Linz geplant. „In den nächsten zehn bis 15 Jahren werden alle klassischen Hochöfen verschwinden. An der Dekarbonisierung der Stahlindustrie führt kein Weg vorbei“, sagt Susanne Michelic, Professorin für Eisen- und Stahlmetallurgie an der Montanuni Leoben. Gänzlich ersetzen können die neuen Öfen die klassischen Hochöfen nicht. Um qualitativ hochwertigen Stahl zu erzeugen, muss dem in den Elektrolichtbogenöfen verwendeten Schrott frisches Roheisen beigemengt werden; dieses entsteht durch den Einsatz von Koks und Kohle im Hochofen – zumindest noch.
Die Zukunft soll dem Wasserstoff-Stahl gehören. In einer Testanlage im steirischen Donawitz laufen derzeit Versuche zur -neutralen Stahlerzeugung. Vereinfacht gesagt werden Kohle und Koks, die im klassischen Hochofen das Eisenerz in Roheisen verwandeln, durch Wasserstoff und elektrische Energie ersetzt. Der Riesenvorteil: Das Nebenprodukt ist Wasser anstatt des klimaschädlichen . In Linz erprobt die voestalpine zudem die Erzeugung von Wasserstoff in industriellem Maßstab.
Die Nase vorn hat beim Wasserstoff-Stahl aktuell Schweden. In dem 1000-Seelen-Dorf Boden im Norden des Landes entsteht derzeit ein Hüttenwerk, das Stahl ausschließlich mithilfe von Wasserstoff produzieren wird. 2025 will das Start-up H2 Green Steel das Werk in Betrieb nehmen. Es wäre eine Weltpremiere. „In Österreich, den USA, Südkorea, Deutschland und anderen europäischen Ländern besteht die Herausforderung darin, den Wasserstoff in bestehende Stahlwerke zu integrieren“, sagt Metallurgin Michelic. Dort werde mit Hochdruck daran geforscht. „Es wird nicht eine Lösung für alle geben, sondern standortspezifische Wasserstoff-Stahlkonzepte.“